the technology
PVD (Physical Vapor Deposition) is a coating under controlled vacuum or atmospheric conditions.
This method permits to coat any material in any shapes,achieving metallized effects extremely resistant and durable over the time
Vision
all PVD Metallization and Sputtering machines are designed and built to allow customers in all sectors:
– higher aesthetic-performance finishes,
– significant reduction in the use of harmful substances, pollution levels and energy consumption
Visione
tutte le macchine PVD Metallizzazione e Sputtering vengono progettate e realizzate per permettere ai clienti di tutti i settori :
– più elevate finiture estetico-prestazionali,
– significativa riduzione dell’utilizzo di sostanze nocive , livelli di inquinamento e consumi energetici
main benefits
- Sustainable and ecological
- Fast process with very low costs
- Low temperature deposition
- No production of harmful waste
- Uniform duplicatable coating, adjustable thickness
- Deco-functional surfaces
- Digital and easy to control process
- Low consumption of material and energy, no use of water (reduced electricity consumption is a strong KPI at the current situation)
- Clean, cold, and dry coating, chemical free
- Deposition of metals and alloys on all surfaces (plastic, glass, metal, ceramic, etc.)
- Compatible with other surface treatments: paint, electroplating, anodic oxidation, cleaning (raw material)
- 3D coatings with maximum design freedom and increased penetration
PVD coatings can fulfill the following purposes: aesthetic, functional, decorative, electronic, antibacterial, reflection, insulation, magnetism, filtration, conductivity, medical, wear, corrosion, mechanical and other.
RELEVANT STRENGHTS
- Environmentally friendly
- Uniform deposition
- Low temperature
- Repeatable
- Multilayer
- Adjustable thicknesses (semi-transparent, full coverage, high thickness)
- Clean Chrome
- No harmful waste
- Functional capacities: transparency to RF, EMI shielding,semi-transparency
- Vastly quicker production time when compared to traditional chrome plating
- Small production footprint
- Minimizes the need for outsourcing
- Maintains the elasticity/flexibility of the piece
- Any material can be coated
- Greater flexibility in the design of the pieces
- Wide range of finishes: colours and brightness, glossy and matt
- Large variety of substrates
- Recyclable
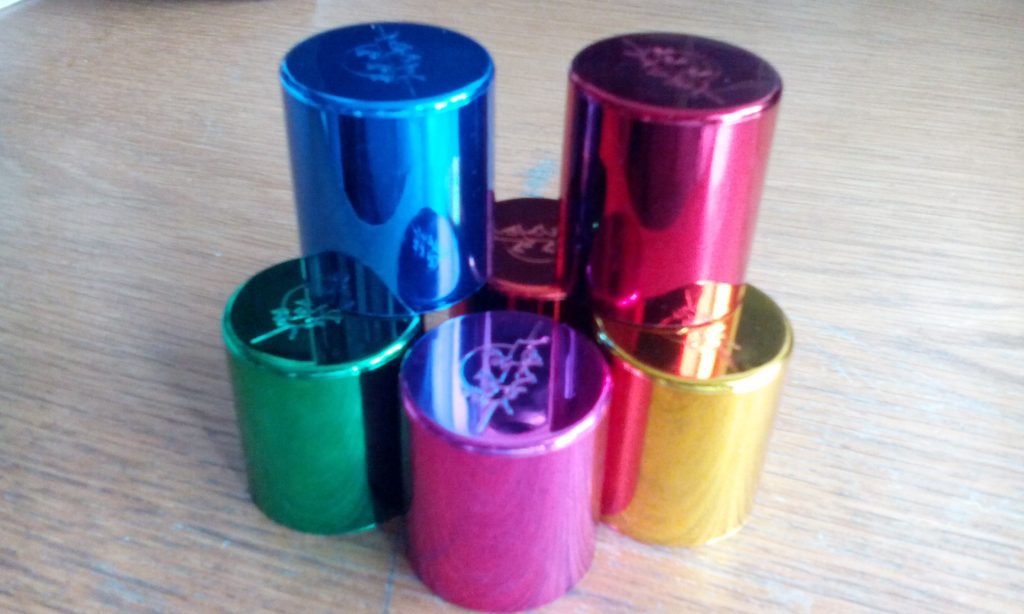
both automotive and solar applications, cosmetic and fashion accessories.
characteristics / finishings
aesthetics
Finishing :
– sparkling, mirror-like
– mat
– tranparent
– iridescence
– semi transparent
– possible painting with all colors
functionals
antibacterial
reflection
insulation
Faraday cage
electro magnetism
filtration
conductivity
medical
wear
corrosion
mechanical
CHROME FINISHING
AF antifinger print
electromagnetic interface
antibacterial protection
conductive surfaces
insulating surfaces
fireproof surfaces
water repellent surfaces
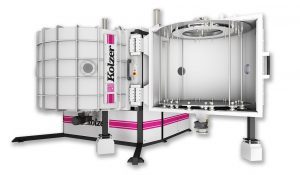
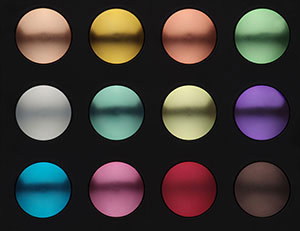
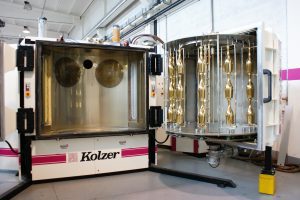
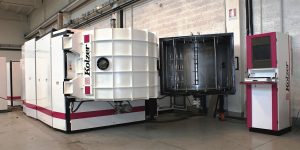
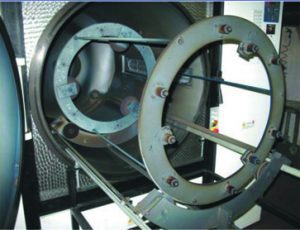
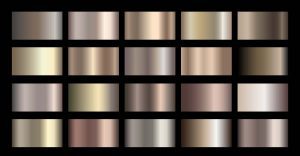
what is
metallization
METALLIZATION Metallization allows to obtain bright or mat metal finishing, evaporating aluminum onto any substrates (glass, plastic, metal, carbon fiber, woood, etc.) with a cold, dry and environmentally friendly cycle. Special iridescence effect.
SPUTTERING : it’s possible to deposit any metal or alloy (chrome, stainless steel, brass, copper, titanium, gold, pure silver, etc) on any material, shape, size and geometry substrate.
Sputtering allows a wide range of original metallic colors
GREEN CHROME
PLATING
TECHNOLOGY
PVD SPUTTERING 2.0
A fundamental premise:
our PVD sputtering machines apply METALLIC CHROME.
From this base we can see the world of chrome plating completely changed:
from a chemical process
to a physical process
NO liquids,
NO tanks,
NO expensive energy,
NO dangerous and expensive disposal as in traditional galvanic technology,
NO large spaces.
One of the most important applications for both environmental and functional purposes is that linked to the chrome plating of both non-ferrous and ferrous metal components.
Also important the application of metallic chrome coating in place of electrolytic baths .
PVD FUNCTIONAL SPUTTERING 2.0
the PVD Functional is better and faster than PVD Arc coating: The new Metal coating uses a special PVD 2.0. process that fixes the roof with a high-density pattern that allows for greater levels of strength and brightness thanks to the molecular structure that mimics the substrate underneath. This makes it more resistant and durable than “standard” PVD. One of its side effects is that it is easier to clean and that it captures fewer fingerprints
plasma
Plasma is a clean, dry process, performed at room temperature, that does not require any cleaning
products nor solvents (no consumable materials).
It is a treatment that allows the removal of surface material forming volatile products.
•It removes organic contaminants or residue layers
•It improves surface tension, and therefore wettability of the surfaces, reducing the angle with
regard to liquids at optimal values
•It sterilizes
•It cleans any surfaces (of any nature, geometry and dimension) and modifies its chemical and
electrostatic characteristics.
PECVD
PECVD is a transparent coating with a barrier effect.
The growth of thin films onto a surface can be efficiently done through chemical reactions in vapor
phase of components containing the element to be deposited.
The result is a new product, with the same mechanical and physical characteristics, but with
different possibilities in interacting with surrounding matter.
This treatment is usually applied in order to improve adhesiveness and wettability properties of
polymers allowing the transformation of a surface, from water-repellent to hydrophilic
Remarkable are the characteristics of hydrophobicity ,oil repellency, resistance to impacts, gas barrier, water repellency, transparency,
With PECVD technology you can achieve similar benefits on all surfaces, metals, alloys, polymer, and plastics, wood, glass, etc.
Grafting, anti-corrosion in acid and alkaline environments, water repellency, oil repellency,
fireproofing, scratch-resistant, non-sticking, anti-printing and bio – compatibility, anti-stain effect
and decrease of water vapor (anti-fog properties), etc
NEWS/MAGAZINE ARTICLES in various languages :
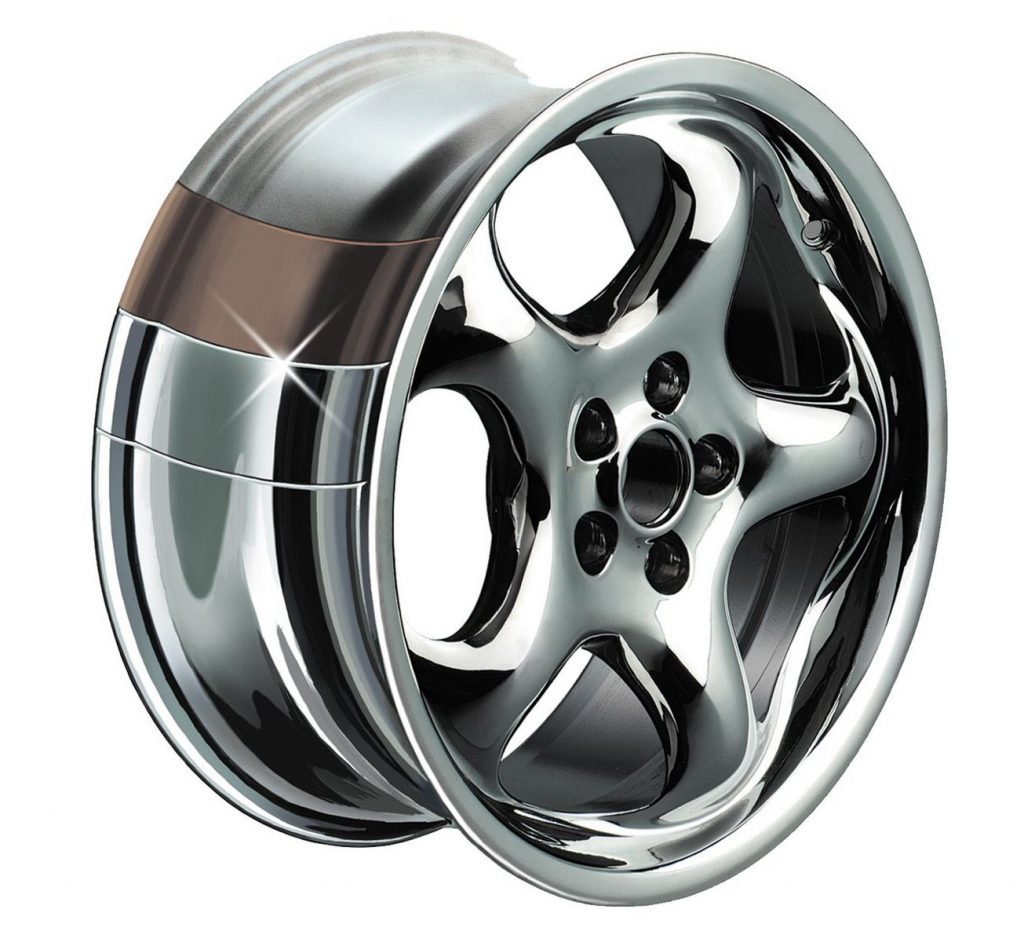
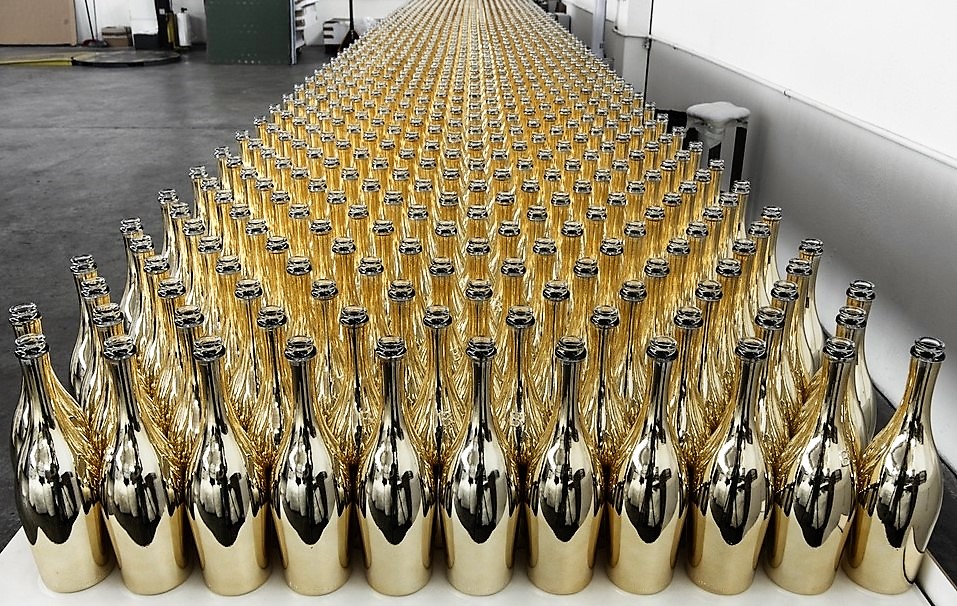
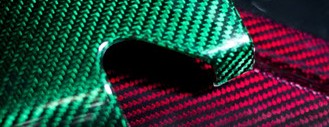
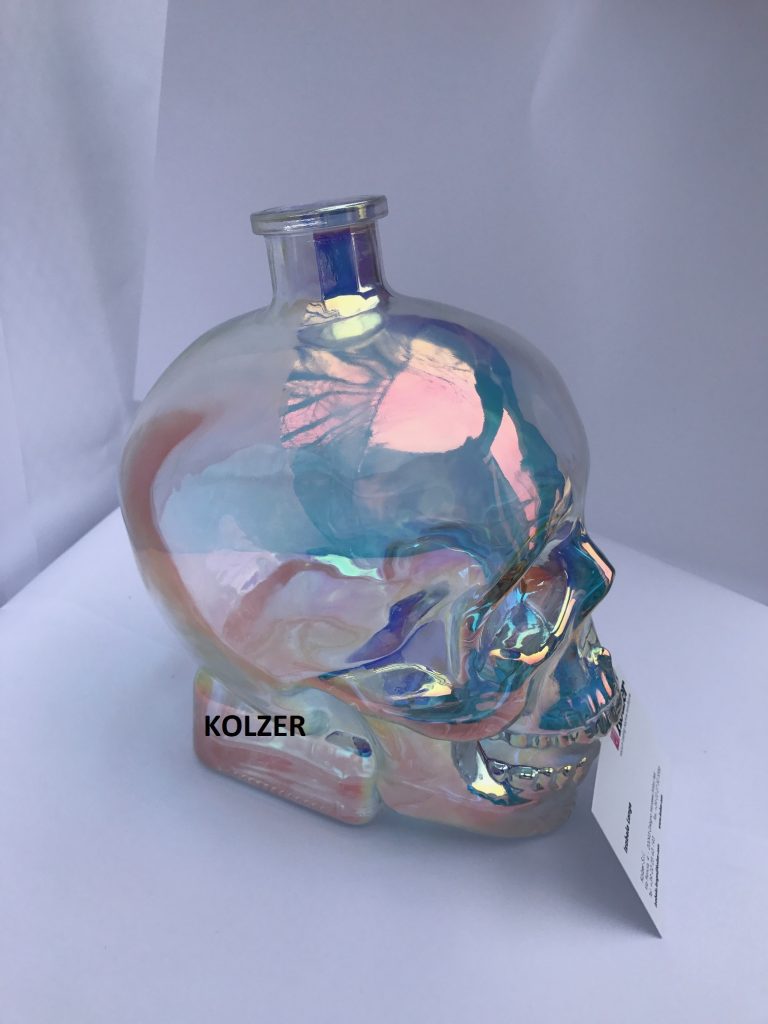